An overview of the bronze casting process
The original sculpture is usually made in a malleable medium, such as clay or wax. A rubber mold is made, and a hard outer mold is made to keep the rubber in shape. (This is an unfinished version of the angel.)
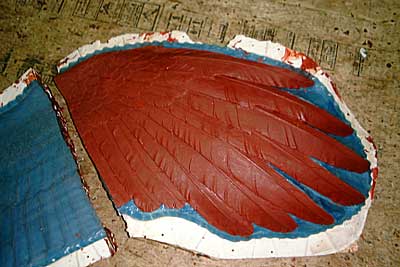
Molten wax is poured into the mold, and becomes the pattern. Imperfections, such as air bubbles are repaired. The blue material in this picture is the rubber mold, and the white is the hard "mother mold" which hold the rubber in shape.
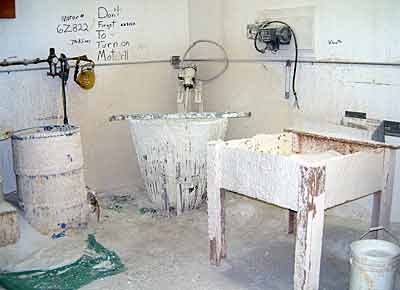
A sticky liquid slurry (center tank) helps bind very fine sand (left tank) to the wax. Coats of coarser sand (right box) are added for strength.
The shell is drilled in many places to allow wax to escape. Hydraulic pressure will crack the shell if the wax cannot escape.
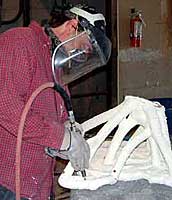
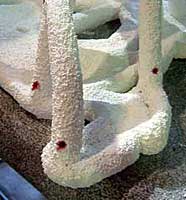
The drilled shells are placed in a hot kiln (1600 plus degrees F.) and the wax melts out. The picture on the right shows flames coming out of the piece. The shells are hollow after this step.
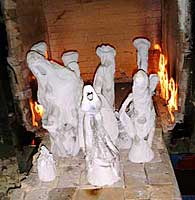
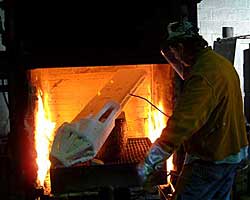
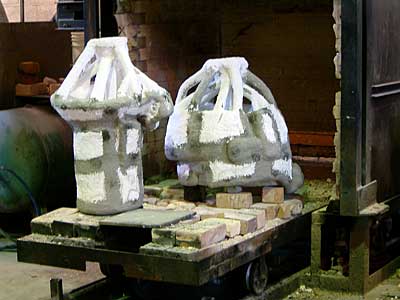
The holes are patched, and refractory cement is added to strengthen the shell. It is put back in the kiln and reheated just prior to pouring bronze.
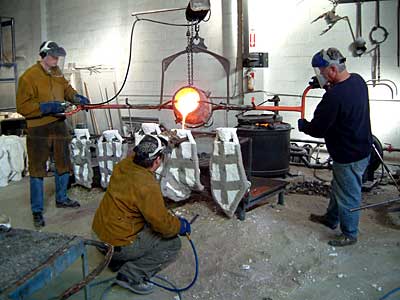
Molten bronze is poured into the hollow shells
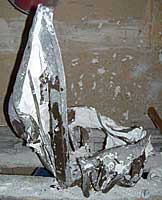
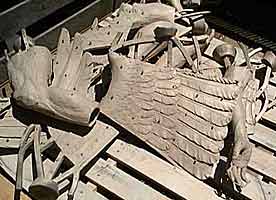
The shell is broken away from the bronze, which is then sandblasted
The bronze is patinaed, and the owner has a thing of beauty which will last a long time.
Please mouse over an image to see a larger picture
Commissions